New catalyst twice as selective, could make chemical production cleaner and cheaper
Researchers demonstrated a new electrically powered catalyst that is twice as efficient as baseline materials at producing acetic acid, which has multiple industrial applications.
By Victoria Martinez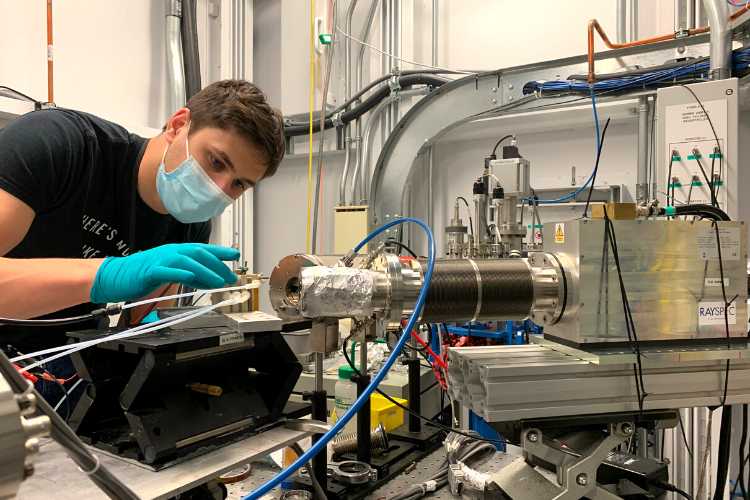
An estimated 18 million tonnes of acetic acid are produced annually around the world for industrial applications like making paints, adhesives and coatings. Now, researchers from the University of Toronto (U of T) have demonstrated a new electrically powered catalyst that is twice as efficient as baseline materials at producing acetic acid. Their research has the added bonus of having a much smaller carbon footprint.
Catalysts are used to help convert raw materials into usable products, but the raw materials used to make acetic acid today are fossil fuel-based, meaning production can have negative environmental impacts. Here, the only inputs are CO2-derived CO, water and renewable electricity.
"In this project, I identified a strategy to design catalysts that might be extremely selective to a single chemical, meaning they produce more of the chemical you want, in this case acetic acid, and much less of the by-product chemicals you don’t want,” says Joshua Wicks, a doctoral student in Professor Edward Sargent's research group at UofT.
"In our lab, we are very interested in the decarbonization of chemicals production and we're always searching for promising opportunities to apply electrochemistry in this hard-to-decarbonize sector of the economy."
The team’s results were published in Nature today.
While other catalysts are composed primarily of copper, the new catalyst is only one percent copper. The copper is surrounded by silver atoms, which provides several advantages – the catalyst is significantly more selective for acetic acid while still operating at scalable reaction rates, and it is also very stable, a boon for industrial applications.
Wicks' colleagues Jun Li and Panos Papangelakis used the SXRMB beamline at the Canadian Light Source of the University of Saskatchewan to study the chemical environment of the catalyst in action. Observing the catalyst before, during and after use helped the team link their theoretical work to what they saw at the CLS.
"We're very lucky in Canada to have access to CLS facilities,” says Wicks. “These are complex experiments, and to study them in real-time with state-of-the-art measurements is not something to be taken for granted."
Once developed to an industrial scale, the new catalyst could make production of an important chemical much cleaner and cheaper.
Jin, Jian, Joshua Wicks, Qiuhong Min, Jun Li, Yongfeng Hu, Jingyuan Ma, Yu Wang et al. "Constrained C2 adsorbate orientation enables CO-to-acetate electroreduction." Nature (2023): 1-6. https://doi.org/10.1038/s41586-023-05918-8
Photos: Canadian Light Source | CLS’ SXRMB beamline used for this research | Research team at the CLS
Media Relations:
Victoria Schramm
Communications Coordinator
Canadian Light Source
306-657-3516
victoria.schramm@lightsource.ca