X-rays allow us to quickly develop high-strength steels
Synchrotron analyses could be used to fast-track the development of novel high-strength steel designs.
By Brian OwensSteel girders
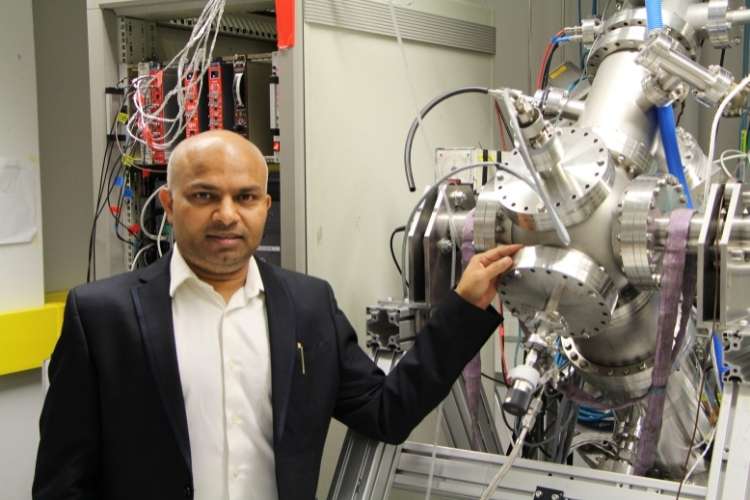
Knowing how strong a piece of steel is, especially the stainless steel used in everything from cars to buildings, is vitally important for the people who make and use it. This information helps to keep people safe during crashes and to prevent buildings from collapsing.
Accurately predicting the strength of a steel prototype based on its microstructure and composition would be indispensable when designing new types of steel, but it has been nearly impossible to achieve — until now.
“Designing/making the best-strength steel is the hardest task,” said Dr. Harishchandra Singh, an adjunct professor at NANOMO and the Centre for Advanced Steels Research at the University of Oulu in Finland.
Estimating the contribution of various factors towards designing high-strength novel steel has traditionally required numerous tests that can take months, according to Singh. Each test also requires a new sample of the prototype.
Instead, Singh and colleagues used the Canadian Light Source (CLS) at the University of Saskatchewan to predict the strength of a novel steel.
They shone the facility’s synchrotron light on a small cube of steel and analyzed the diffraction pattern it produced as the powerful X-rays passed through it. This created data on the crystal structure of the steel that the researchers used to predict its material properties, including strength, through an analytical model.
The team found that these predictions matched up exactly with the data from time intensive, traditional lab-based tests.
The team’s method offers a new way to predict the yield strength for highly alloyed complex steel. The process could also help to engineer novel steels through a better understanding of the relationship between a steel’s microstructure and its mechanical properties.
Not only was the synchrotron-based method for analyzing steel just as reliable as traditional testing, but it was much faster and required far less material.
“We can get complete information about the crystalline microstructures from the synchrotron in one hour, rather than spending a couple of months on various lab-based testing,” he said. Their findings were published recently in the Journal of Materials Research and Technology.
This rapid and accurate synchrotron-based method of testing could be extremely helpful to the steel industry to approximate the strength of the developed steels and could save months compared to standard routes, said Singh.
“Steel companies make hundreds of batches of steel. With synchrotron testing, they could have precise results from every batch the same day,” he said.
Going forward, steel developers can use synchrotron analyses to quickly and accurately predict the strength of novel steel prototypes and use the data to help identify what elements of a prototype are beneficial or not. This faster method for assessing and developing steel could lead to better building materials coming on the market.
Ghosh, Sumit, Shubo Wang, Harishchandra Singh, Graham King, Yi Xiong, Tian Zhou, Marko Huttula, Jukka Kömi, and Wei Cao. "Quantitative prediction of yield strength of highly alloyed complex steel using high energy synchrotron X-ray diffractometry." Journal of Materials Research and Technology (2022). https://doi.org/10.1016/j.jmrt.2022.07.066.
Photos: Synchrotron | BXDS beamline used for this project | Dr. Singh and co-authors
Media Relations:
Victoria Schramm
Communications Coordinator
Canadian Light Source
306-657-3516
victoria.schramm@lightsource.ca